3 Mil Fusion Finesse Polypropylene Laminate
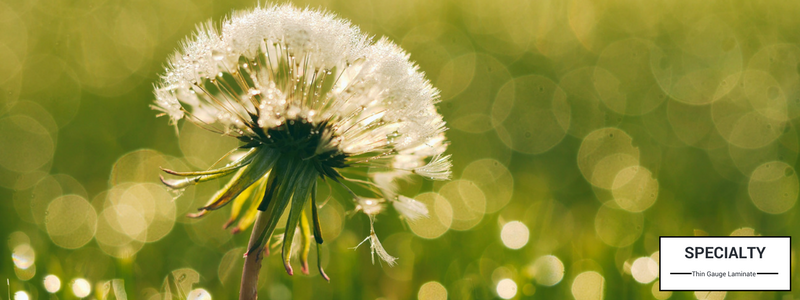
3 Mil Fusion Finesse Polypropylene Laminate is a versatile, pressure-sensitive, laminating film that can be used to economically produce a wide range of graphics on less costly cold-roll laminators. Made from a proprietary co-polymer film, it is more rigid and has less curl than vinyl films. It also doesn’t yellow, and may appeal to environmentally-conscious customers who prefer to use PVC-free materials. With a price point equivalent to thermal laminating films, 3 Mil Fusion Finesse can be used to produce graphics for banner stands, trade-show displays, and POP signage.
Benefits | Applications | Customers |
---|---|---|
|
|
|
SPECIFICATIONS | |
---|---|
Material Type | Clear semi-gloss co-polymer film |
Thickness | 3 mil |
Adhesive | 001” (25 micron) high clarity, high performance acrylic pressure sensitive adhesive. |
Release Liner | .004” (100 micron) poly-coated 2 side bleached kraft paper |
Gloss Level | target 30, range 25 – 35 |
Tensile Strength | (ASTM D-882): 4800 – 5300 psi |
Elongation | (ASTM D-882): 900 - 1100% |
Peel Adhesion | (PSTC-1): 20 minute dwell = 50 oz./in. |
Shear Strength | (PSTC-7): 1” x 1” panel, 1000 gram load, 96 hours with no failure |
Inkjet Media Preparation | Recommend that you allow your print to dry for a minimum of 24 hours before lamination. In areas with high humidity dry times can be longer. |
Laminator Compatibility | Compatible with most hot and cold laminators. The laminator should be equipped with a release liner take-up roller. |
Laminator Setting | For best results, the following guidelines should be followed: top & bottom laminator rollers should be set to 100°F (38°C). This softens the adhesive allowing for better conformation to the substrate. Nip pressure should be set to 80# - 100# psi, and line speed should be 2-3 feet per minute. Heavy nip pressure is necessary for thick gauge laminates to ensure a consistent bond to the substrate. Slower run speeds are necessary to avoid entrapment of air within the lamination. The top and bottom web tension should be low to medium to prevent curling of the panel. A rigid sled at least .125” (3.175mm) composed of a hard surface such as Masonite, acrylic or aluminum should be used to guarantee consistent pressure across the web. Before lamination occurs the finished print must dry for a minimum of 24 hours. |
Finishing | After applying the laminate, allow the panel to lay flat for a minimum of 2 hours cure time before cutting, trimming or rolling. Ideally, the lamination should be allowed to cure for 24 hours prior to trimming and rolling. When trimming graphics, always cut the softer, thinner material first. With a freshly sharpened blade, cut using a straight edge on tempered glass. Shipping/storage tubes should be ideally 12” diameter, but never less than 10” diameter. Before lamination occurs the finished print must dry for a minimum of 24 hours. |
Core Size | 3 in |
Optimal Service Environment | -30°F to 160°F |
Min. Application Temperature | 50°F |
Ideal Storage Conditions | 50-85°F, 40-80% R.H. (a controlled environment is recommended); store in original packaging. |
Shelf Life | 1 year from the ship date when stored in proper conditions. |
SKU | Size |
---|---|
UFF38150 | 38" x 150 ft. |
UFF51150 | 51" x 150 ft. |
UFF61150 | 61" x 150 ft. |
Datasheet
Product Performance & Suitability: All of the descriptive information and recommendations should be used only as a guide. Furnishing such information and recommendations shall in no event constitute a warranty of any kind. All purchasers shall independently determine the suitability of the material for the purpose for which it is purchased. Seller’s and manufacturer’s only obligation shall be to replace such quantity of the product proved to be defective. Neither the seller nor manufacturer shall be liable either in tort or in contract for any loss or damage, direct, incidental or consequential (Including loss of profits or revenue) arising out of the use of or the inability to use the product. No statement or recommendation not contained herein shall have any force or effect unless in agreement signed by officers of seller and manufacturer.
Updated 3 months ago